Discover how industrial automation and connectivity improve production
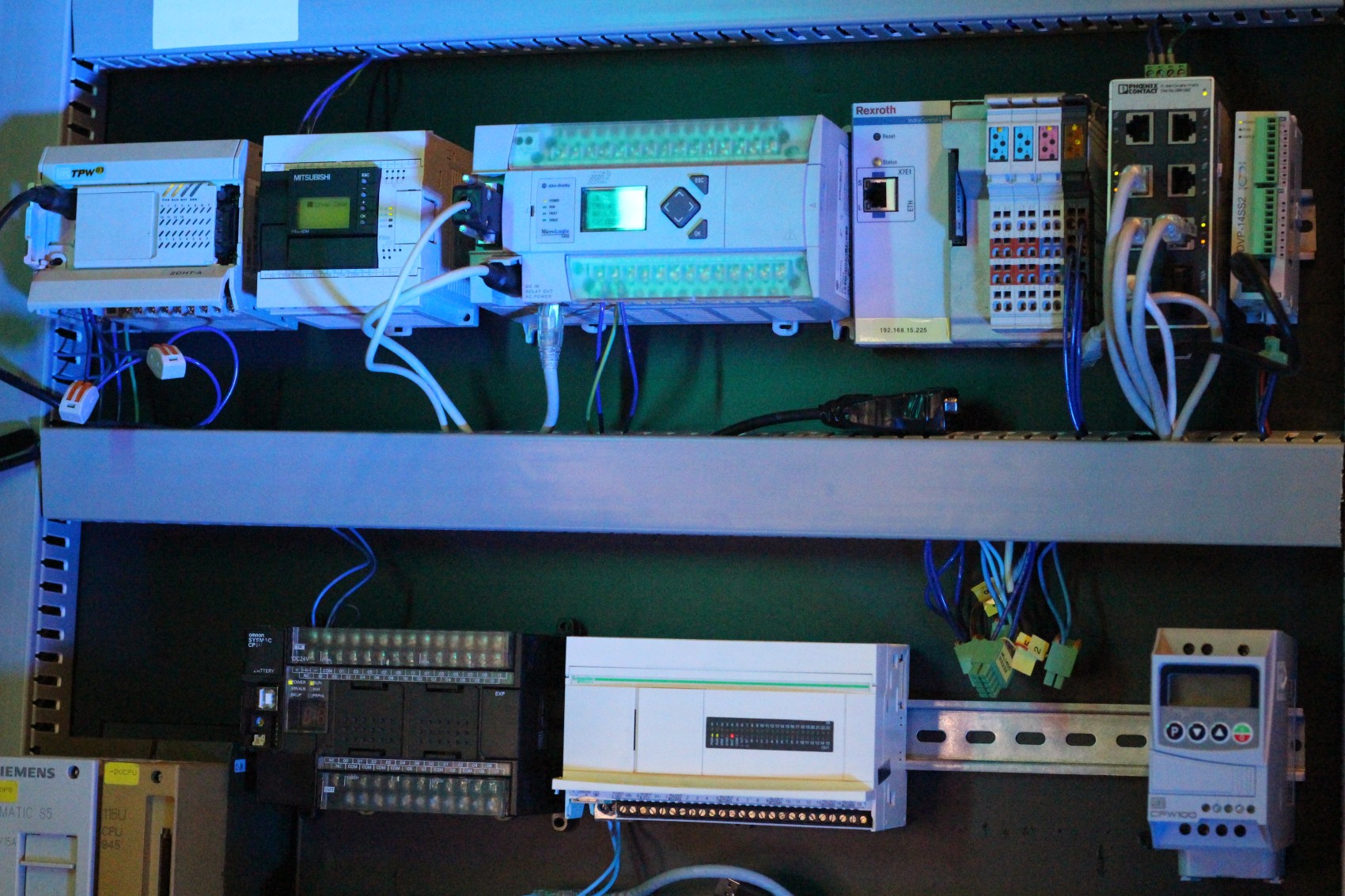
Copyright: ST-One
Following the motto of increasing productivity, Henry Ford (1863-1947) idealized the so-called “assembly line”, which was the real drive for the beginning of mass production. In the years following Ford’s death, General Motors and other industries already had automated relay machines. However, due to its complex programming, in 1968, the company BedFord Associates was hired to develop what would become the first Programmable Logic Controller (PLC).
With increasingly complex and decentralized processes, it was necessary to find a way to facilitate the control of industrial plants. Standardizations of the most intelligent instruments were created, so that their maintenance would be low-cost and easily disseminated. This is how industrial communication networks and standards emerged.
This is important for interoperability, which is the ability of different systems, devices, and software to communicate and exchange information effectively. Standardization ensures consistency in this communication, as it ensures that systems are developed within recognized practices.
Get to know industrial automation standards
Industrial automation standards are sets of standards that establish procedures for the integration, operation, and maintenance of automation systems in industry. They cover everything from communication between devices to the human-machine interface (HMI) and process control and monitoring methods. Within the HMI framework, standards establish rules for the design, functionality, and operation of interfaces. These include guidelines on the presentation of information, screen navigation, use of graphics and colors, and the management of alarms and notifications.
The main purpose of these standards is to improve integration between operators and automation systems, ensuring that interfaces are understandable and easy to use. When combined with data analysis, they are essential in the quality analysis process, as they minimize operational errors.
In short, they contribute to:
- Usability: standardized interfaces are more intuitive and easier to use, reducing the learning curve for operators.
- Security: standards ensure that interfaces present information clearly and consistently, avoiding erroneous readings.
- Consistency: standardization ensures that all interfaces follow the same guidelines, facilitating the integration of new systems and maintenance of existing ones.
- Quality: clear and well-organized interfaces improve the stability of the production line, enhancing the quality of the production process.
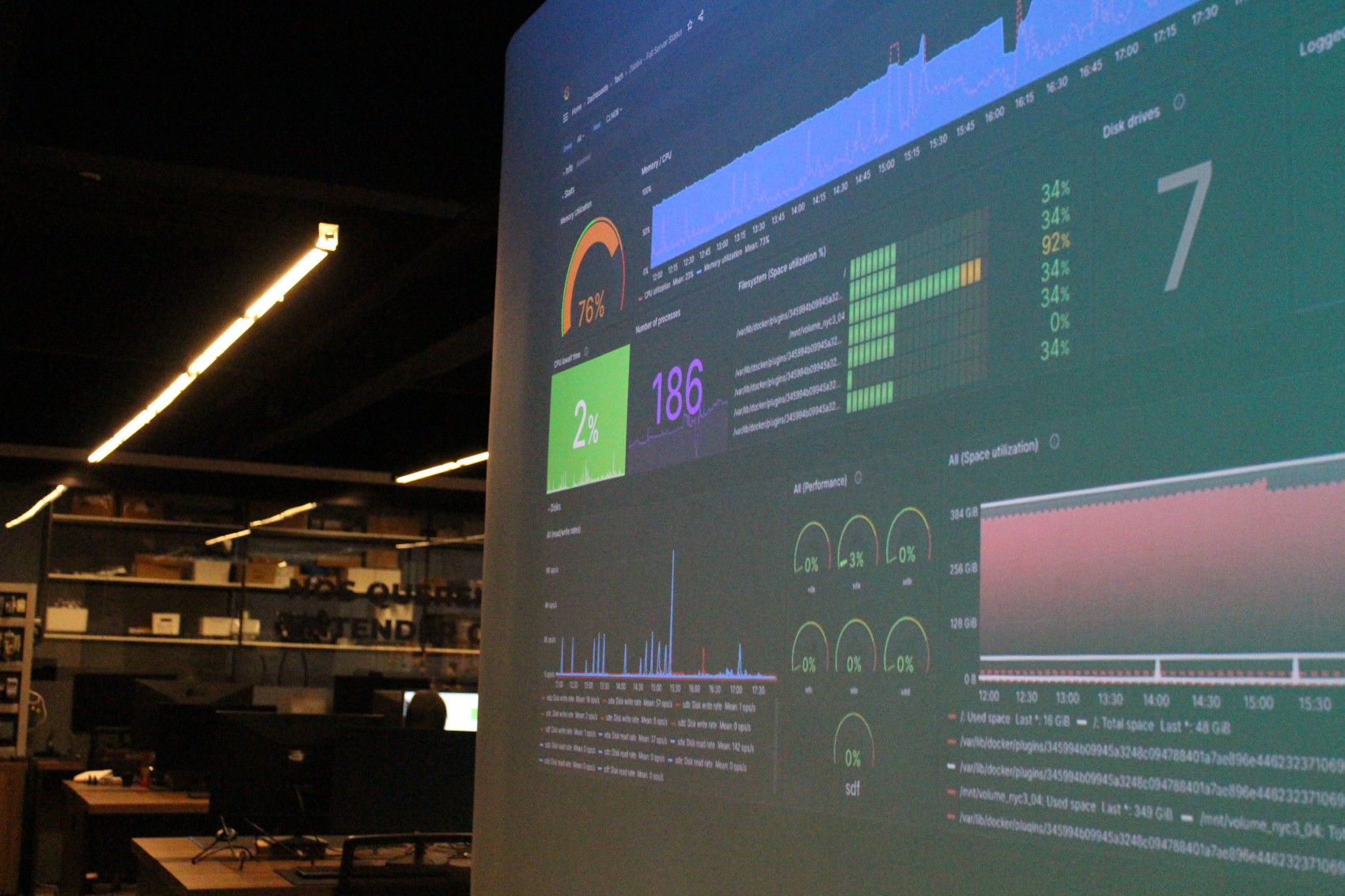
Copyright: ST-One
ML Pack: Packaging Control
Among the many examples of technical automation standards is PackML, created by the Automation and Machine Control Organization (OMAC) in the early 2000s. The main focus of its development was to standardize and generate consistency for all the machines that make up a packaging line (or other discrete processes). The need for regulation arose from the fact that machines used proprietary interfaces and control methods, making it difficult to integrate and efficiently operate production lines composed of equipment from different suppliers.
Three categories were created to systematize the production of this machinery. PackSoft was focused on programming language; PackConnect for communication protocols; and PackML to unite the previous two. This means that PackML provides quick integration of the production line without the need to worry about which communication protocol will be responsible for transmitting the data between the machines.
To achieve this, this standard includes state templates such as “Stopped,” “Running,” and “Under Maintenance,” which makes it easier to communicate and control. It also includes the so-called Packtags, which are standardized tags for data included in the machine state. They are used in M2M (machine-to-machine) communication, for example, between a filler and labeler. Finally, they contribute to OEE (Overall Equipment Effectiveness) calculations by indicating performance parameters. After going through several versions, the official document that gathers the guidelines was implemented in the report “ANSI/ISA-TR88.00.02-2008 Machine and Unit States: An Implementation Example of ISA-88”.
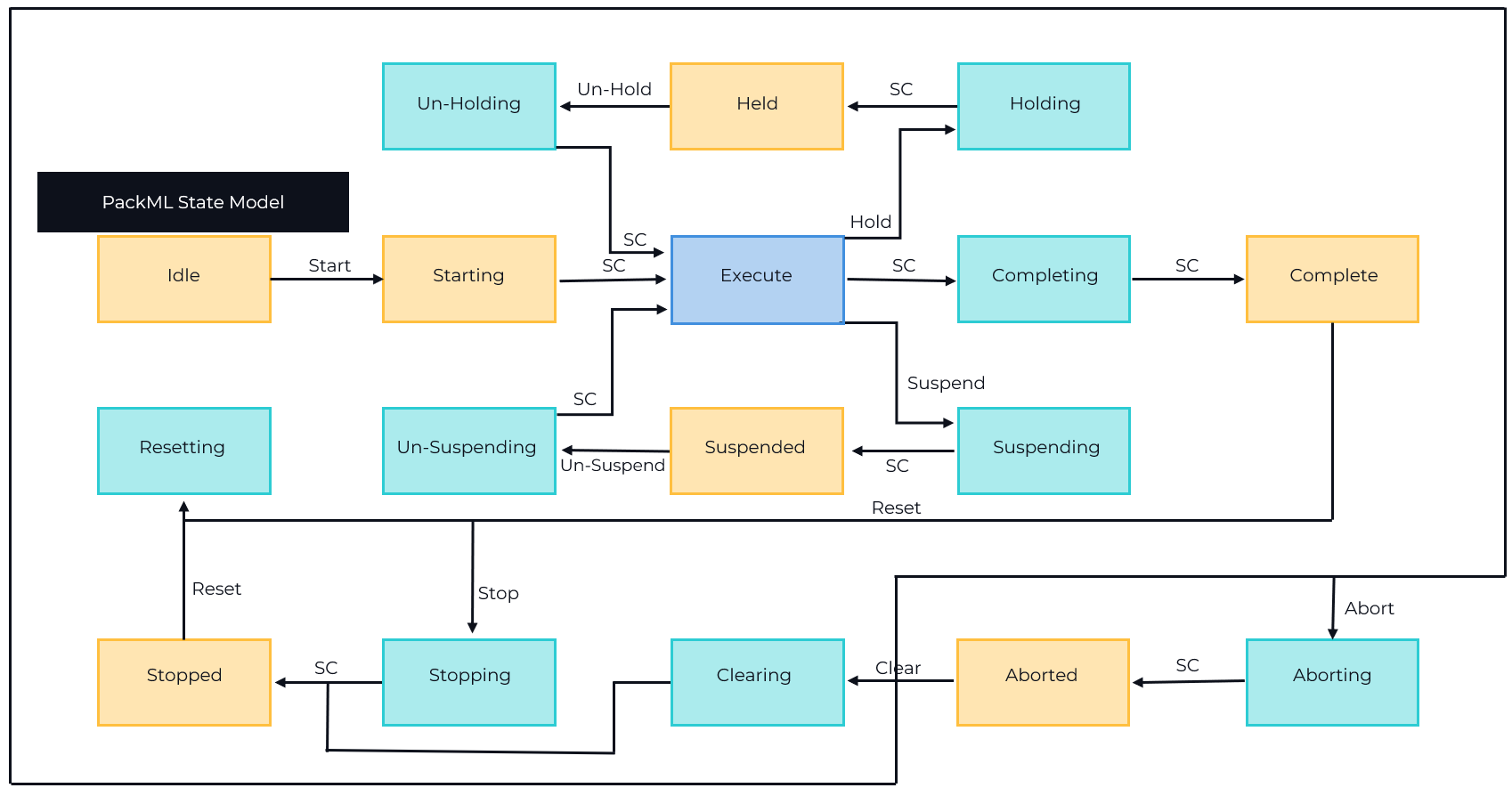
Copyright: ST-One
What is Weihenstephan Standards (WS) and what is its importance
The Weihenstephan Standards were developed under the guidance of the Technical University of Munich (TUM) by the Food Packaging Technology course in the 2000s. The group responsible was composed of machine manufacturers, plant managers, IT system developers, technologists, among others.
Also known as WS, they are standardized communication interfaces for collecting data from machines in industry. These standards define the uniform transmission of data from machines to IT systems such as Supervisory Control and Data Acquisition (SCADA) and Historian. This is done by specifying the physical interface, its content, and recommendations for data assessments and reporting.
The physical interface specifies how data is physically transmitted between devices. This interface is equipped with content that defines what data should be transmitted and how it should be structured. This includes guidelines on how data should be analyzed and reported to improve decision-making.
The standardization of data is done through tags that specify different states and modes of operation of the machines, they are:
- WS_state: indicates the current state of the machine (e.g. in operation, stopped, under maintenance).
- WS_Mode: specifies the machine’s mode of operation (e.g., automatic, manual).
- WS_Prog: identifies the active program or process (e.g., production cycle, cleaning cycle).
Weihenstephan Standards allow multiple data points, such as operating states and error codes, to be consolidated into a single machine state. They also contribute to interoperability and operational efficiency. This feature facilitates real-time monitoring and informed decision-making.
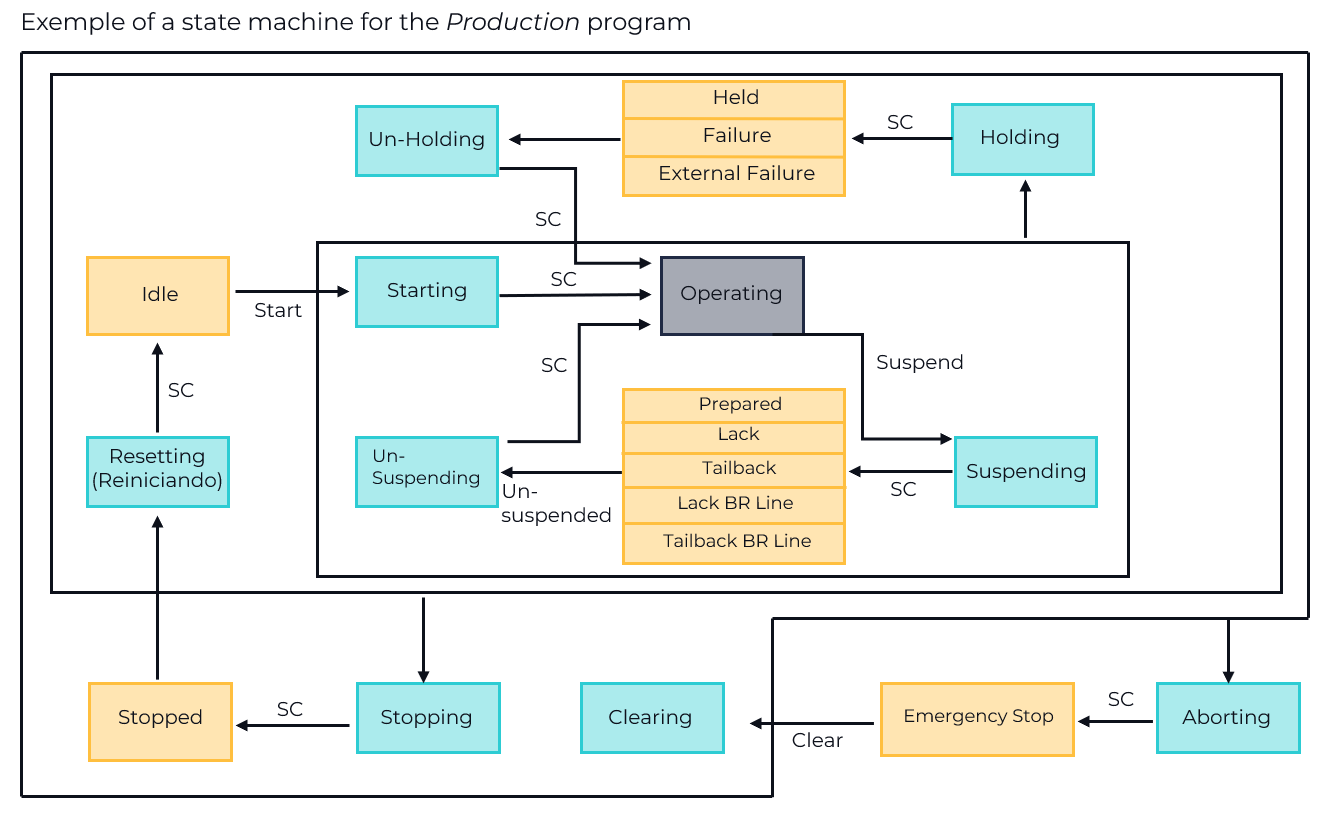
Copyright: ST-One
Technologies that improve industrial automation
The so-called connected industries, or smart industries, have several technologies that complement and improve industrial automation.
One of them is the Internet of Things (IoT), which accelerates the adoption of internet-connected technologies among industries. IoT is made up of Internet Protocols (IP) and Transmission Control Protocols (TCP). These parameters form the sensors, devices and systems that allow these smart devices to communicate with each other and with other internet-enabled devices. The connectivity provided by the sensors installed in the industrial plant allows the continuous collection of operational data. This constant collection is essential to monitor and control processes according to Weihenstephan and PackML standards. Also, communication between different machines ensures integrated information that allows for better understanding.
The Historian system, on the other hand, is a type of database specialized in simultaneously collecting, storing, and analyzing large volumes of data from industrial processes. In it, data such as temperatures, pressure, speed, among others, are recorded over time. This system provides continuous monitoring of industrial processes, including using the Weihenstephan and PackML standards to unify the way of visualizing and understanding the operation of machines over time. Additionally, having a data history is essential at the time of analysis, as it helps to understand trends according to the patterns found.
Finally, data science is a field that encompasses the collection, analysis and interpretation of large volumes of data generated during the operation of the lines. It is intrinsically linked to IoT technologies and intuitive visualization of information. Standardizing information with PackML and WS results in an analysis with fewer errors and that provides valuable insights to reduce costs, increase productivity, and optimize production. Also, an intuitive interface with well-defined signs helps in maintenance, by quickly detecting anomalies.
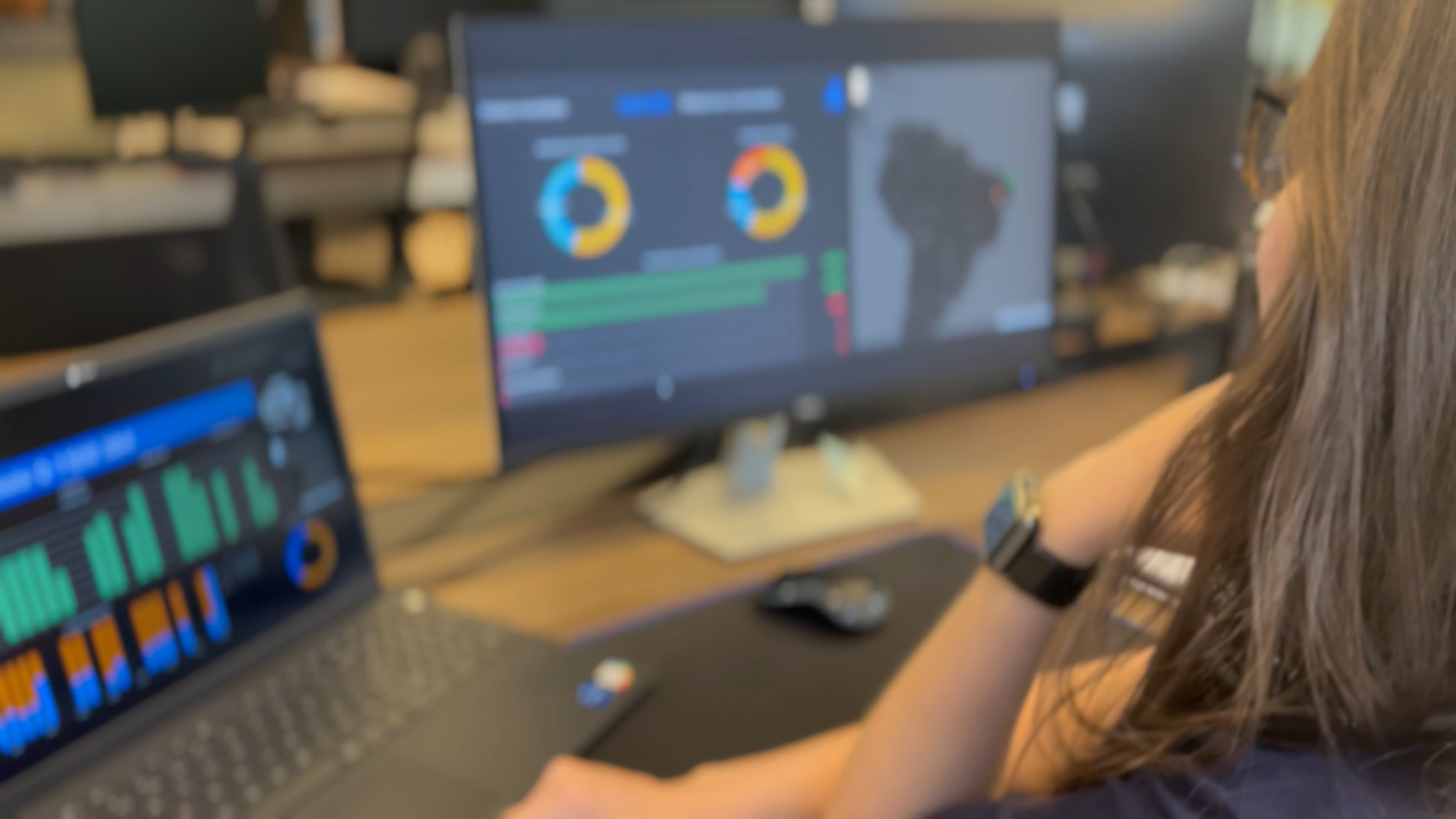
Copyright: ST-One
Application of standards in industry
Industrial automation standards — such as Weihenstephan Standards and PackML — are applied in the most diverse sectors of manufacturing industry, resulting in several benefits:
- Performance analysis: WS are used to connect machines from different manufacturers, allowing for the collection and analysis of production data. For example, a brewery can use WS to monitor the performance of filling lines and identify bottlenecks in production.
- Quality monitoring: WS helps ensure the consistency and quality of the final product by monitoring critical parameters during the production process, such as temperature and pressure.
- Process optimization: In the bakery industry, WS can be used to automatically adjust fermentation times based on humidity and ambient temperature. This results in better quality control and operational efficiency.
- Machine integration: PackML standardizes the communication interface between machines and production lines, facilitating the integration of new equipment. For example, a food factory can use it to integrate a new packaging machine with the existing system, reducing downtime and improving efficiency.
- Process control: The PackML standard allows for continuous monitoring and control of production processes such as packaging and labeling. This helps ensure product consistency and compliance with food safety regulations. Get to know ST-One.