Os fornos industriais são peças fundamentais da produção em diversas indústrias, desde a metalurgia até a panificação, desempenhando papéis essenciais na transformação de materiais por meio do calor. Cada tipo de forno possui características próprias, projetadas para atender às necessidades específicas de seu setor.
Na metalurgia e siderurgia, os fornos de indução usam campos eletromagnéticos para fundir metais de forma eficiente, garantindo uniformidade térmica e qualidade estrutural. O controle da frequência do campo eletromagnético e da temperatura é essencial para manter a uniformidade no aquecimento, evitando deformações ou falhas estruturais. Já na indústria cerâmica e de vidro, os fornos de alta temperatura operam acima de 1600°C, permitindo fusões e vitrificações essenciais para resistência e durabilidade dos produtos. Para manter a qualidade de produção é comum o monitoramento da pressão interna e da temperatura.
No setor químico e farmacêutico, os fornos elétricos proporcionam um controle preciso da temperatura, garantindo esterilizações seguras e processos químicos estáveis. A eficiência energética é crucial aqui, monitorada através do consumo elétrico e da estabilidade térmica.
A indústria alimentícia e de panificação depende dos fornos de lastro, que, com suas pedras refratárias, asseguram cocção uniforme e textura ideal em pães e confeitaria. O controle da temperatura da pedra e da umidade é essencial para a qualidade final dos produtos.
Por outro lado, os fornos a gás são amplamente usados na produção de ligas metálicas e na sinterização de cerâmica, destacando-se pelo rápido alcance de altas temperaturas e eficiência térmica. O fluxo de gás e a temperatura são monitorados para maximizar a combustão e o desempenho.
Forno Túnel na indústria alimentícia: controle e melhoria contínua
Na indústria alimentícia, a produção em larga escala exige processos térmicos contínuos, padronizados e controláveis. O forno túnel é peça central nesse cenário, especialmente em linhas de produção de biscoitos, onde conecta a modelagem da massa ao empacotamento final.
O processo começa com a massa moldada sendo transportada por uma esteira através do forno, dividido em zonas térmicas com funções específicas.
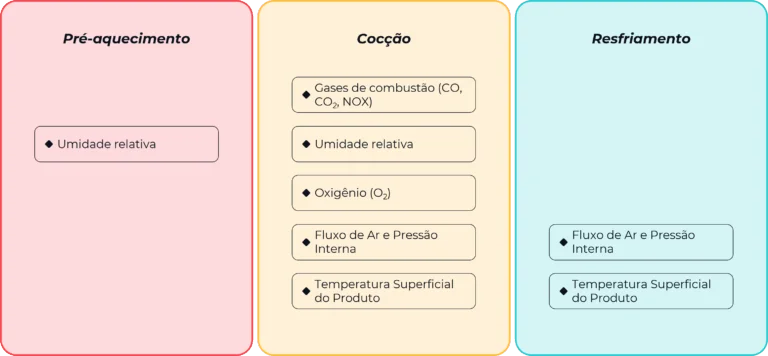
A primeira é a zona de pré-aquecimento, que eleva gradualmente a temperatura do produto, promovendo a evaporação da umidade superficial e prevenindo choques térmicos que poderiam afetar a estrutura do biscoito. O controle da umidade aqui é essencial para preservar a integridade da massa.
Em seguida, vem a zona de cocção, onde ocorrem as principais transformações físico-químicas: gelatinização do amido, expansão de gases, evaporação da água interna e formação da crosta. Essa zona é subdividida com controle individual de temperatura superior e inferior, permitindo ajustes conforme o tipo de produto. Em fornos a gás, sensores monitoram gases de combustão e oxigênio para garantir segurança e eficiência. Sensores de fluxo de ar e pressão mantêm a uniformidade térmica, assegurando padronização.
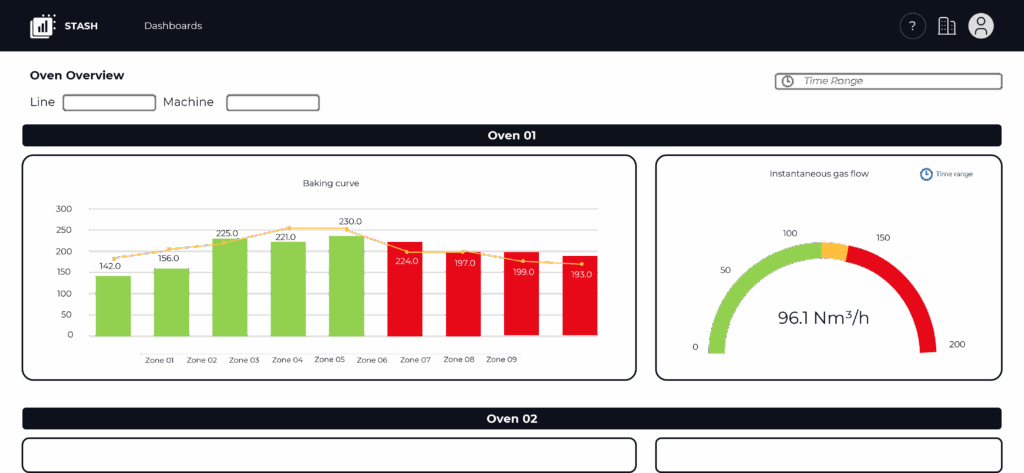
Após a cocção, os biscoitos passam pela zona de resfriamento, que reduz a temperatura de forma controlada para evitar condensações e deformações. O resfriamento pode ser natural ou forçado, e sensores garantem que os biscoitos atinjam a temperatura ideal para o empacotamento.
A eficiência do forno túnel depende da coleta de variáveis assertiva, controle PID e análise de dados em tempo real, o que possibilita otimização energética, manutenção preditiva e rastreabilidade da qualidade.
Cada etapa do forno túnel desempenha um papel estratégico, desde o preparo da massa até o resfriamento final, garantindo um produto padronizado e de alta qualidade.
Forno Túnel na indústria cerâmica: da sinterização a qualidade dimensional
Na indústria cerâmica, a fabricação de louças sanitárias, como bacias, exige um processo térmico rigoroso e contínuo. O forno túnel contínuo é o equipamento central, conduzindo as peças por um ciclo completo — da secagem final à vitrificação — assegurando estabilidade dimensional, resistência mecânica e bom acabamento superficial.
As peças cruas são carregadas em vagonetes que percorrem lentamente o interior do forno. A primeira etapa, de pré-aquecimento, eleva a temperatura gradualmente até cerca de 600 °C. Nessa fase, remove-se a umidade residual e ocorrem reações de decomposição de compostos orgânicos. O controle da taxa de aquecimento, da umidade relativa e da exaustão de gases voláteis é essencial para evitar trincas, fissuras e deformações nas peças.
Em seguida, as peças entram na zona de queima, onde a temperatura atinge de 1200 °C a 1250 °C. É aqui que ocorrem as principais transformações: a sinterização da massa cerâmica e a vitrificação do esmalte. Essa zona é segmentada com pontos de controle independentes, utilizando sensores para monitorar temperatura, fluxo de ar, pressão interna e composição dos gases de combustão (CO, CO₂, NOx). Sondas de oxigênio otimizam a eficiência da queima, especialmente em fornos a gás. A velocidade dos vagonetes é ajustada conforme o perfil térmico necessário, garantindo o tempo de residência ideal.
Na etapa final, o resfriamento controlado reduz a temperatura das peças até cerca de 100 °C, de forma gradual, evitando choques térmicos que possam comprometer a integridade estrutural. Ventiladores com controle de vazão e sensores de temperatura garantem que as peças atinjam condições seguras antes da saída do forno.
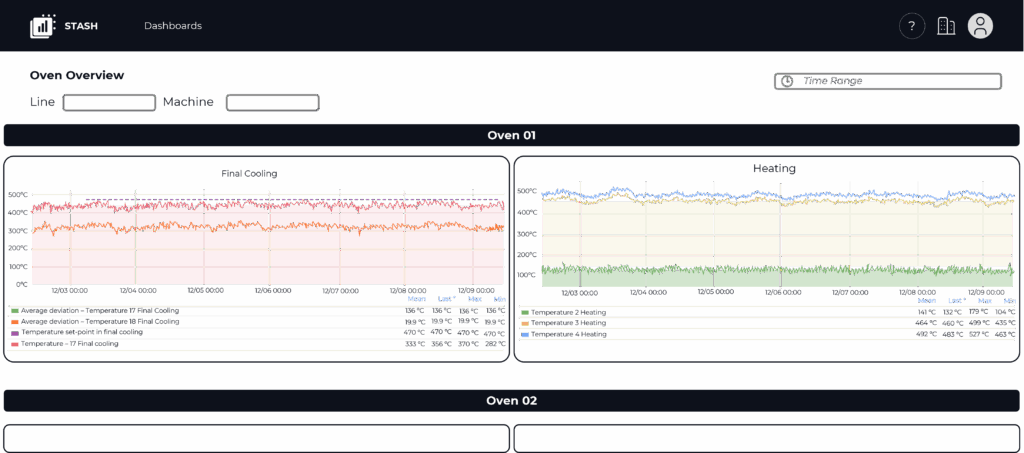
Curva térmica, atmosfera e energia: paralelos entre fornos da indústria alimentícia e cerâmica
Apesar das diferenças em temperatura, tempo de residência e natureza dos produtos processados, os setores alimentício e cerâmico compartilham fundamentos técnicos comuns em engenharia de processos, controle de qualidade e eficiência operacional, permitindo análises integradas e estratégias similares de otimização.
Um dos aspectos centrais é o desenvolvimento da curva térmica e do perfil de aquecimento. Em ambos os casos, a modelagem e o controle da curva térmica são essenciais para maximizar a eficiência energética e reduzir defeitos. Ferramentas como simulações térmicas, análise de gradientes de temperatura e controle PID distribuído são amplamente aplicáveis, com o objetivo comum de garantir que o produto atinja os parâmetros críticos de transformação — seja a cocção de alimentos ou a sinterização de cerâmica — sem falhas estruturais.
Curvas Térmicas Típicas em Fornos Túnel: Biscoitos x Louça Sanitária
Outro ponto fundamental é a distribuição térmica e sua uniformidade ao longo do forno. A homogeneidade do ambiente térmico é avaliada por meio de mapeamento com sensores distribuídos, uso de câmeras infravermelhas e simulações por CFD (dinâmica de fluidos computacional). Essa análise reduz variações de qualidade entre diferentes posições do forno ou entre lotes, promovendo maior padronização.
A eficiência energética também é um objetivo compartilhado. A medição do consumo por unidade de produto, associada à análise de perdas térmicas e estratégias como recuperação de calor, permite reduzir custos operacionais e emissões, mesmo diante de escalas térmicas distintas.
Por fim, o controle da atmosfera interna do forno é crítico em ambos os setores. O monitoramento da composição de gases — como O₂, CO, CO₂ e umidade relativa — evita reações indesejadas, como oxidação ou ressecamento, e assegura a estabilidade e repetibilidade do processo produtivo.
Controle em forno industrial e ESG: eficiência e responsabilidade
Segundo a CNN Brasil (2024), os investimentos com foco em ESG — critérios ambientais, sociais e de governança — já representam mais de um terço dos ativos sob gestão global, com projeções que apontam para US$ 53 trilhões até 2025. Empresas com desempenho insatisfatório nesses critérios enfrentam dificuldades para atrair investidores, uma vez que os relatórios de ESG são usados como referência-chave nas decisões de investimento. Dados da SAP reforçam essa tendência: em 2022, 69% das grandes indústrias na América Latina já possuíam estratégias ESG em execução.
Nesse contexto, a análise e o controle de variáveis em fornos industriais, especialmente a temperatura, desempenham papel estratégico. No pilar ambiental (Environmental), o controle preciso da temperatura contribui diretamente para a eficiência energética, reduzindo o consumo de combustíveis e, consequentemente, as emissões de gases como CO e CO₂. Isso favorece o cumprimento de normas ambientais, como a ISO 14064, e reforça o compromisso com práticas sustentáveis.
No aspecto social (Social), a operação segura e estável dos fornos reduz riscos de acidentes, superaquecimentos e falhas que podem comprometer tanto a integridade dos colaboradores quanto a qualidade do produto. A conformidade com padrões como a ISO 9001 fortalece a reputação da empresa perante clientes e parceiros.
Já na governança (Governance), o monitoramento contínuo das variáveis térmicas e a transparência na divulgação de dados operacionais são fundamentais. Relatórios alinhados a padrões como o GRI e o SASB demonstram responsabilidade corporativa e reforçam a confiança de stakeholders.
Analisar variáveis térmicas em fornos industriais, portanto, vai muito além da eficiência operacional: é uma prática central na construção de uma indústria mais sustentável, segura e transparente.