Análise de temperatura em fornos: qualidade e ESG na indústria
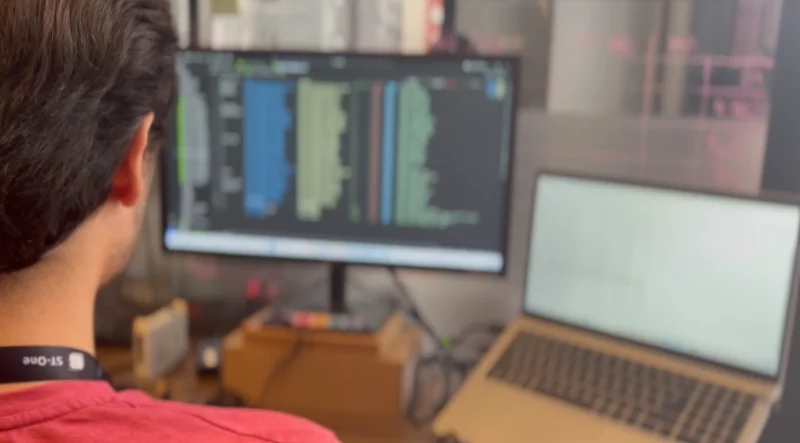
- Sumário
Análise de temperatura em fornos: qualidade e ESG na indústria
Tipos de fornos para cada setor da indústria manufatureira
Importância da análise de temperatura
Tipos de análise de temperatura em fornos industriais
Controle de temperatura e ESG: qual a relação?
Análise de temperatura em fornos: qualidade e ESG na indústria
Os fornos industriais desempenham um papel crucial em diversos setores da manufatura, sendo essenciais para processos de aquecimento, moldagem secagem e tratamento de materiais. A utilização desse maquinário é antiga, tendo seu surgimento datando a China Antiga, durante a Dinastia Shang (1600-1046 a. C.). Um pouco depois, na Dinastia Han (206 a.C. – 220 d.C.), ele era capaz de atingir temperaturas de até 1200º para a produção de ferro fundido. Já na Grécia e Roma Antiga, eles eram construídos com câmaras separadas para a queima e ventilação, o que aprimorou o controle da temperatura durante o processo. Essa técnica foi desenvolvida para a produção de cerâmica e vidro.
Essa evolução continuou na Idade Média, pois, na Europa Medieval, a construção dos fornos de alvenaria começou a ser feita utilizando tijolos e telhas, o que também permitia o controle do calor e da fumaça. Nessa época, o foco era a produção de metais e vidro.
Com o advento da Revolução Industrial, a invenção do forno a carvão por Jordan Mott em 1833 e de ferro fundido marcaram um avanço significativo. Isso por serem mais eficientes e permitirem a produção em larga escala. Também, em 1826, o forno a gás foi patenteado, tornando-se um item comum nas residências e indústrias no século XX.
Após isso, houve a introdução dos fornos elétricos, criados em 1882 pelo canadense Thomas Ahearn, o que revolucionou a indústria. A nova invenção permitiu o controle preciso da temperatura, além de ser mais segura e eficiente. Em fornos a gás, esse mesmo processo acontece através do ajuste da quantidade de gás e ar fornecidos aos queimadores. Atualmente, os fornos industriais utilizam tecnologias avançadas, como fornos de indução e de atmosfera controlada, para processos específicos que exigem alta precisão e eficiência enérgica.
Tipos de fornos para cada setor da indústria manufatureira
Cada processo possui uma necessidade específica, pois cada produto requer condições específicas de temperatura e atmosfera para sua produção. Essa característica justifica a variabilidade de fornos utilizados na indústria manufatureira, como:
- Indústria metalúrgica: nesse setor, os fornos mais usados são os de arco elétrico, de indução e fornos de resistência. O primeiro utiliza arco elétricos para atingir altas temperaturas rapidamente e fundir metais em grandes quantidades. Já os fornos de indução realizam um aquecimento rápido sem contato direto com o material. Isso é ideal para a fusão de metais não ferrosos no qual a pureza do material é importante. Por último, os fornos de resistência são comuns em tratamentos térmicos e de recozimento, em que a precisão de temperatura e uniformidade no aquecimento são cruciais;
- Indústria alimentícia: os fornos de túnel industriais são os mais utilizados na secagem, torrefação e processamento térmico dos alimentos. Eles permitem a produção em massa e o cozimento uniforme de alimentos como biscoitos e torradas. Com longos túneis, os produtos são transportados através de diferentes zonas de temperatura;
- Indústria química: são utilizados em processos de calcinação, sinterização e decomposição térmica para a fabricação de produtos químicos. Aqui, os fornos rotativos utilizam cilindros para aquecer materiais uniformemente. Já os de tipo de leito fluidizado transferem calor através de partículas fluidizadas, garantindo eficiência térmica;
- Indústria automotiva: utilizado no tratamento térmico de componentes automotivos como endurecimento de peças metálicas e cura de revestimentos. Assim, são utilizados fornos de atmosfera controlada para evitar reações indesejadas como a oxidação;
- Indústria cerâmica e vidro: os fornos realizam a queima da cerâmica, fusão e moldagem do vidro e tratamento térmico para endurecimento. Nesse caso, são utilizados fornos de fusão ou túnel, onde o controle preciso da temperatura em cada zona garante a qualidade do produto e evita quebras;
Importância da análise de temperatura
O relacionamento entre inovação e qualidade é estreito. De acordo com dados do IBGE (2021), 70,5% das indústrias com mais de 100 funcionários inovaram em 2021. Esse número se explica, pois, a qualidade está diretamente relacionada com atender as necessidades e expectativas individuais dos clientes. Assim, no processo de gestão, é preciso implementar mecanismos inovadores que atestem a qualidade do processo produtivo, para, consequentemente, conseguir se manter competitivo no mercado.
Para gerenciar os processos, garantir a qualidade e tomar decisões com maior precisão, precisa-se explorar as informações geradas no processo, como a temperatura da operação, buscando interpretá-las de maneira precisa. Para isso, usam-se tecnologias e ferramentas que coletam, processam e permitem a visualização dos dados de forma clara para identificar inconsistências e aprimorar a qualidade dos processos.
Além disso, o monitoramento de indicadores de temperatura atua em questões de eficiência enérgica, permitindo economia de energia e redução de custos operacionais.
A importância desse tipo de análise também reside no cumprimento de estratégias de ESG. A temperatura dos fornos está intimamente relacionada com a emissão de gases causadores do efeito estufa. Esse controle minimiza a liberação de gases como Monóxido de Carbono (CO) e Dióxido de Carbono (CO₂). Isso contribui para a conformidade com normas ambientais, como a ISO 14064, e o desenvolvimento sustentável nos processos industriais.
Por último, a coleta de dados de temperatura contribui para controlar a vida útil dos equipamentos, reduzindo a necessidade de manutenção frequente e demais custos associados. A menor necessidade de manutenção resulta em uma maior consistência de produção. Durante a reprodutibilidade, processos que requerem temperaturas específicas, dependem de um controle rigoroso para garantir que cada lote de produção atenda aos padrões de qualidade. São alguns deles fusão de metais, sinterização de cerâmicas e cozimento de alimentos.
Tipos de análise de temperatura em fornos industriais
- Indústria alimentícia
A análise de temperatura dos fornos está presente em processos como cozimento de biscoitos, torradas e pães. Também é utilizado durante a pasteurização, para eliminar patógenos sem comprometer o sabor e a textura dos alimentos.
Isso resulta em mais controle de qualidade, ao correlacionar variações de temperatura com defeitos no produto final. Em um forno de túnel, cada zona de assamento possui uma função específica no preparo da receita. Nas zonas de pré-aquecimento, a massa se expande, então o controle de temperatura afeta diretamente na pesagem da embalagem final.


- Indústria mineradora e metalúrgica
Durante a extração de minerais, os fornos são utilizados na calcinação, para separar e remover impureza dos minérios. Posteriormente, para a fusão dos metais, ele é utilizado para refino e produção de metais utilizáveis.
A análise de temperatura dos fornos ajuda na previsão de manutenção. Como exemplo, padrões de aumento gradual de 5ºC na temperatura média do equipamento precede falhas no revestimento refratário.
- Indústria cerâmica
Nesse setor, o ajuste da temperatura durante a queima da cerâmica evita rachaduras e garante a uniformidade dos produtos. Também, durante a esmaltação esse indicador é essencial para obter aderência e acabamento.
Além do foco em qualidade, tem-se um a otimização dos processos ao analisar dados históricos para melhorar ciclos de aquecimento e resfriamento. O ajuste dos parâmetros de temperatura para redução de tempo aumenta a produção sem comprometer a qualidade.

- Indústria química
Os fornos são usados na destilação, onde o ajuste de temperatura é essencial para separar componentes químicos com precisão. Esse controle também evita reações químicas indesejadas.
É possível correlacionar períodos de alta eficiência enérgica com condições operacionais. Como exemplo, é possível pensar que operar o forno durante a noite consome menos energia devido a menores perdas térmicas para o ambiente externo.

Controle de temperatura e ESG: qual a relação?
De acordo com a CNN Brasil (2024), os investimentos voltados para ESG — com indicadores ambientais, sociais e de governança — representam mais de um terço do total de ativos sob gestão. A tendência é de crescimento, podendo chegar a US$ 53 trilhões (aproximadamente de R$ 273 trilhões) até 2025. Ainda segundo o mesmo canal jornalístico, organização com classificações ruins de ESG podem encontrar barreiras ao buscar investimento externo. Isso acontece porque os relatórios das agências de classificação são usados por investidores como ponto-chave para suas decisões. Esse fato se conecta com outro dado. Segundo a SAP (2022), em 2022, 69% das grandes indústrias na América Latina já possuíam uma estratégia de ESG em execução. O controle de indicadores de temperatura contribui para esse cenário.
Na parte ambiental (Environmental), o controle preciso da temperatura ajuda a reduzir o consumo de energia, o que diminui as emissões de gases de efeito estufa. Além disso, a eficiência energética contribui para a conservação de recursos naturais e a minimização do impacto ambiental das operações industriais.
No social (Social), manter a temperatura adequada nos fornos industriais melhora a segurança dos trabalhadores ao prevenir riscos de superaquecimento e acidentes industriais. Ademais, como já citado, a qualidade do produto final é garantida, ajudando a cumprir normas como a ISO 9001, o que fortalece a reputação da empresa.
Por último, no âmbito da governança (Governance), o monitoramento contínuo e a transparência dos dados de temperatura são essenciais. Organizações que adotam práticas de monitoramento rigorosas demonstram compromisso com a conformidade regulatória e a responsabilidade corporativa. A divulgação de dados confiáveis através de relatórios de sustentabilidade é uma prática recomendada por padrões internacionais. O GRI (Global Reporting Initiative) e o SASB (Sustainability Accounting Standards Board) são exemplos disso. Conheça mais análises aplicadas em cenários reais da indústria química voltadas para ESG.