O primeiro Controlador Lógico Programável (CLP) foi criado em 1969 por Dick Morley e sua equipe na Bedford Associates, atendendo à necessidade da General Motors por um sistema de controle mais flexível e reprogramável do que os tradicionais painéis de relés. O resultado foi o Modicon 084, marco inicial da automação industrial moderna. Com arquitetura modular e lógica baseada em software, o CLP substituiu circuitos eletromecânicos por programação digital, otimizando manutenção, reduzindo custos e aumentando a adaptabilidade dos processos.
Desde então, os CLPs evoluíram com maior capacidade de processamento, integração em redes industriais e suporte a linguagens padronizadas. Nesse cenário, os padrões técnicos são essenciais para garantir interoperabilidade, segurança e eficiência. O destaque é o IEC 61131-3, que define cinco linguagens de programação — LD, FBD, ST, IL (obsoleta) e SFC — promovendo portabilidade entre plataformas. Já o IEC 61131-2 trata dos requisitos elétricos e ambientais dos CLPs.
Além dos padrões gerais, há os de aplicação específica, que adaptam a automação às demandas de cada setor. O Pack ML padroniza estados de máquinas e é comum no setor de embalagens. Os Weihenstephan Standards (WS) organizam a coleta de dados em comumente nos setores de alimentos, bebidas e farmacêutica. ISA-88 e ISA-95 são usados no setor automotivo para controle por lote e integração com sistemas de gestão. Já o IEC 61850 é aplicado em energia, padronizando a comunicação entre dispositivos de proteção e controle.
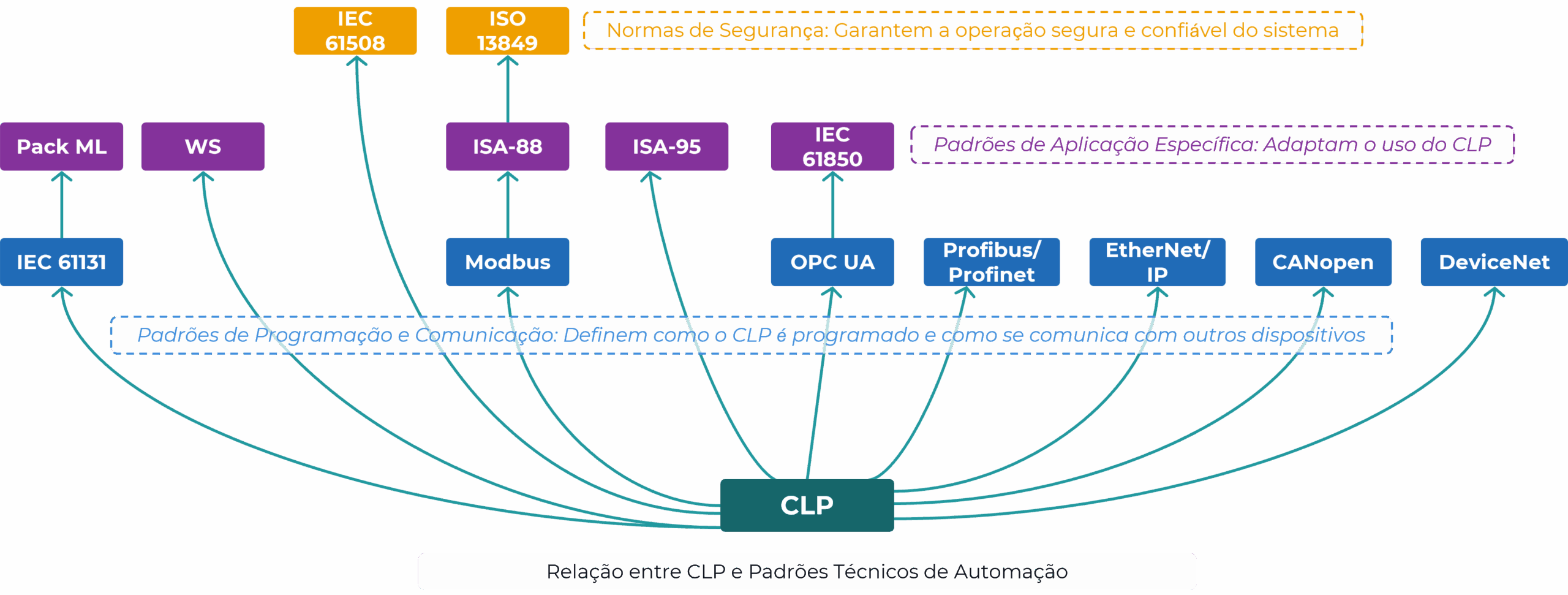
No campo da comunicação, protocolos como Modbus, Profibus/Profinet, EtherNet/IP, CANopen, DeviceNet e OPC UA são amplamente utilizados para conectar CLPs a sensores, atuadores, IHMs e sistemas supervisórios, garantindo troca de dados confiável e em tempo real.
Por Dentro da Máquina: Pack ML
O Pack ML (Packaging Machine Language) é um padrão técnico desenvolvido pela OMAC com base na norma ISA-TR88.00.02, voltado à padronização do comportamento operacional e da comunicação entre máquinas. Seu objetivo é estabelecer uma linguagem comum entre equipamentos, independentemente do fabricante ou da plataforma de automação utilizada.
Esse padrão define um modelo de estados operacionais, como:
- Idle: Estado de repouso, aguardando comando para iniciar.
- Starting: A máquina está se preparando para entrar em operação.
- Execute: Estado ativo de produção ou operação normal.
- Stopping: Processo de parada controlada da máquina.
- Aborted: Interrupção inesperada ou falha crítica.
- Resetting: Processo de recuperação após uma falha.
- Held: Pausa intencional, geralmente por intervenção do operador.
- Suspended: Pausa automática por condições externas.
Esses estados organizam o ciclo de vida da máquina com base na estrutura de dados PackTags, que padroniza variáveis de status e controle, facilitando a integração com sistemas supervisórios. A modularidade do Pack ML também permite o uso de blocos de função reutilizáveis, otimizando o desenvolvimento e a manutenção de software.
Um exemplo prático é uma linha de produção de bebidas com enchedora, rotuladora, seladora e empacotadora de diferentes fabricantes. Com Pack ML, todas seguem o mesmo modelo de estados e estrutura de dados, permitindo integração plug-and-play, interface padronizada e monitoramento unificado. Isso reduz o tempo de comissionamento, facilita o treinamento e melhora a análise de desempenho, como o cálculo de OEE (Overall Equipment Effectiveness).
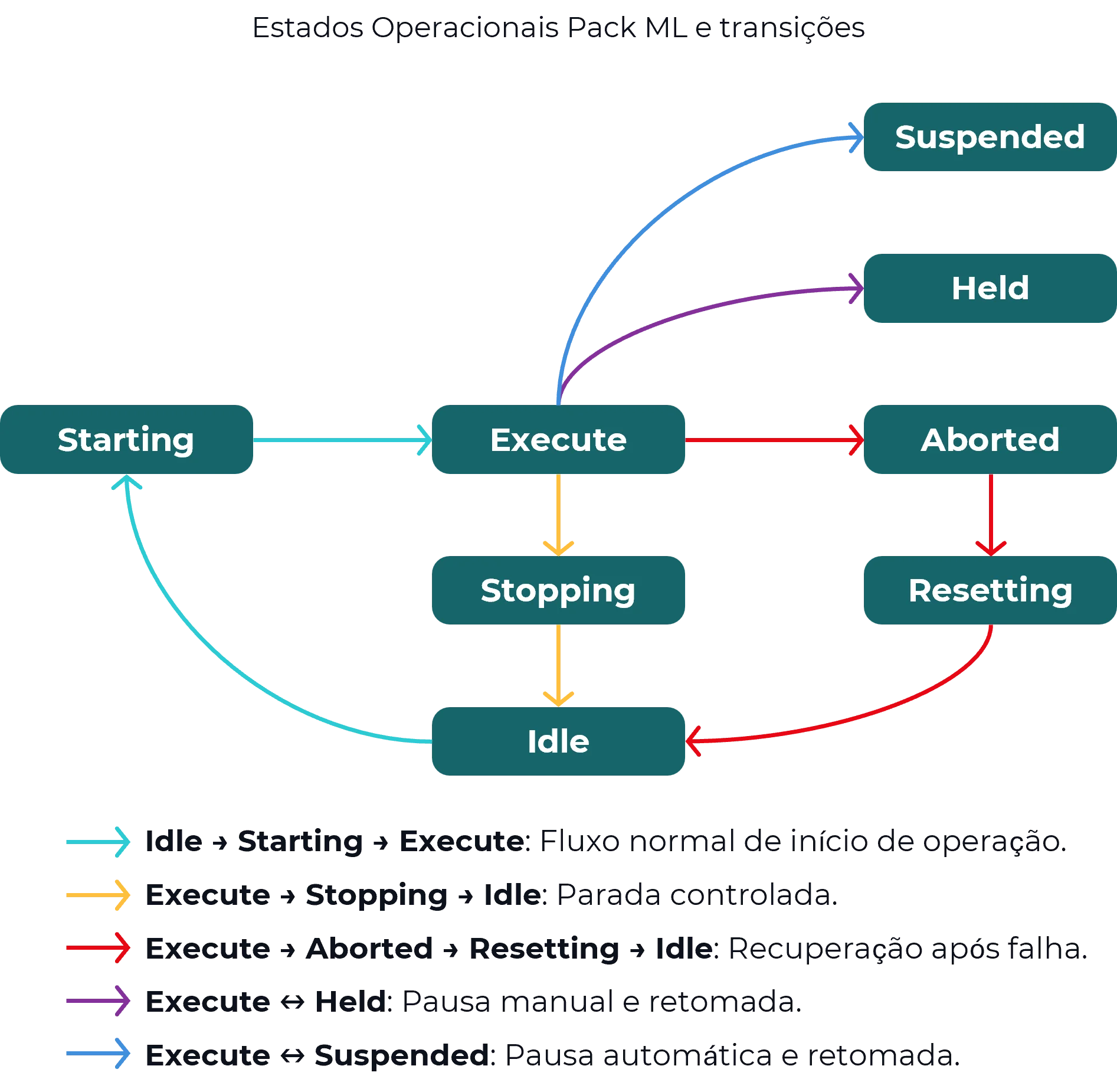
Este formato de organização permite uma separação clara e automatizada entre os tempos de produção ativa (Execute), paradas planejadas (Held, Stopping) e não planejadas (Aborted, Suspended). Isso garante que os indicadores de disponibilidade, desempenho e qualidade sejam calculados com maior precisão, refletindo causas de perda de eficiência e facilitando ações corretivas.
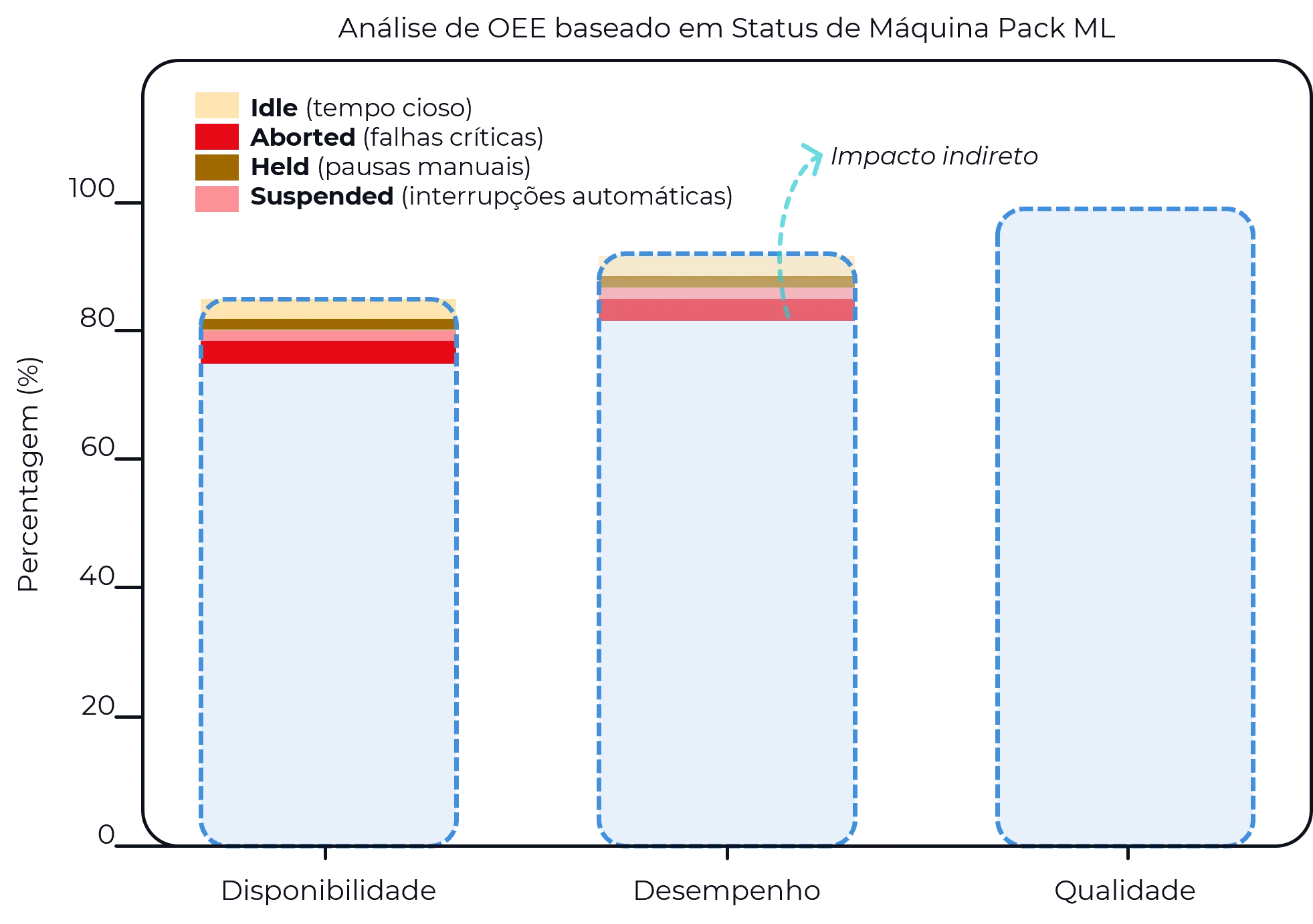
A padronização também permite diagnósticos mais confiáveis, comparabilidade entre linhas e automação da coleta de dados.
Por Dentro da Máquina: Weihenstephan Standards (WS)
Os Weihenstephan Standards foram desenvolvidos sob orientação da Universidade Técnica de Munique (TUM), com foco em setores como alimentos e bebidas. Os WS estabelecem como os dados devem ser adquiridos e transmitidos das máquinas para sistemas de nível superior.
Um dos pilares dos WS é a definição de mais de 440 pontos de dados padronizados, organizados por perfis de máquina específicos por setor industrial. Esses perfis — como WS Pack (envase e embalagem) e WS Food (alimentícia) — garantem que cada tipo de máquina forneça exatamente os dados necessários para controle e análise, de forma estruturada e consistente. As versões mais recentes dos WS adotam o modelo de informação OPC UA, o que amplia a interoperabilidade, segurança e escalabilidade.
Cada ponto de dado representa uma informação da operação, como status da máquina, contadores de produção, tempos de operação, dados de qualidade, informações de lote, modos de operação e alarmes. Esses dados são agrupados por mais de 150 classes de máquina, com pontos obrigatórios e opcionais.
O ponto de dado Machine Status indica se a máquina está em operação. Esse status alimenta diretamente análises de desempenho e decisões operacionais em tempo real. Os estados padronizados nos WS incluem:
- Produzindo: operação normal, produtos válidos sendo fabricados.
- Setup: preparação para novo lote ou produto.
- Standby: máquina pronta, mas aguardando comando.
- Parada não planejada: falhas ou interrupções inesperadas.
- Parada planejada: manutenções ou limpezas programadas.
- Desligada: fora de operação, fim de turno ou manutenção.
- Modo Manual: operação sob controle direto do operador.
- Modo de Manutenção: intervenções técnicas em andamento.
- Alarme/Falha: condição crítica que exige ação imediata.
A organização dos estados da máquina — feitas em códigos padronizados (e.g. 0 = Produzindo, 1 = Parada planejada, etc.), sinais booleanos (e.g. MachineRunning = true/false) ou strings descritivas (e.g. “Producing”, “Idle”, “Error”) — impacta diretamente a eficiência da linha produtiva e o cálculo do OEE:
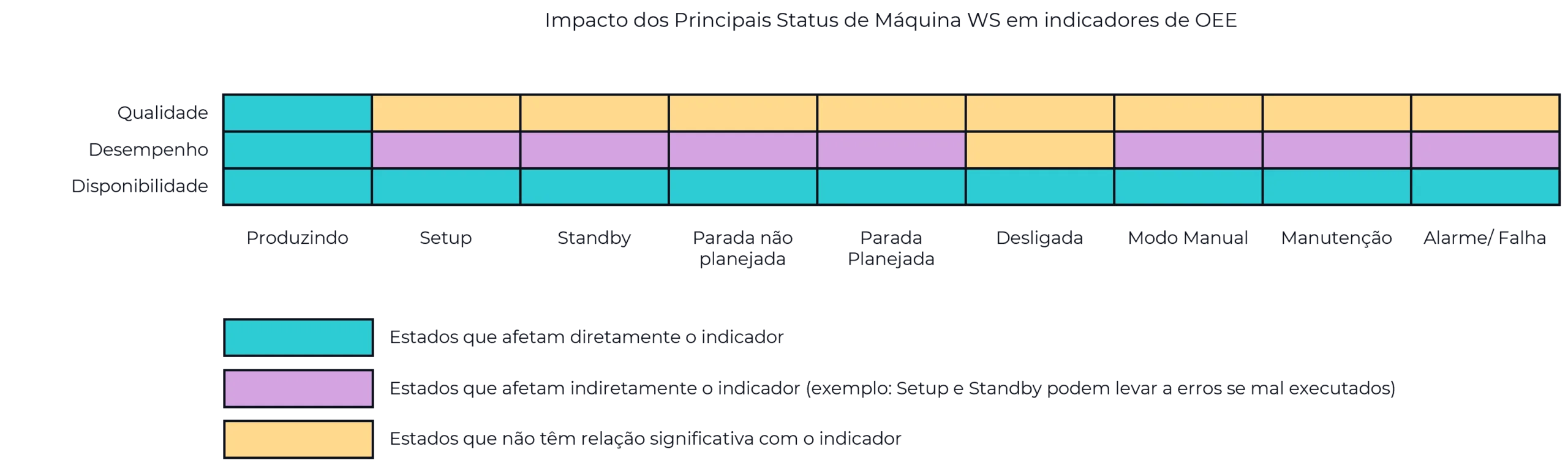
Do Dado à Decisão: Comparativo entre WS e PackML
Indústrias conectadas utilizam tecnologias como IoT para integrar sensores, sistemas e dispositivos via protocolos IP e TCP, permitindo coleta contínua de dados operacionais. Essa conectividade, alinhada aos padrões PackML e Weihenstephan, garante padronização, interoperabilidade e controle em tempo real. Sistemas como Historian armazenam e analisam grandes volumes de dados, registrando variáveis ao longo do tempo para diagnósticos precisos.
A ciência de dados, aplicada sobre essa base padronizada, entra no fluxo para gerar insights e otimizar o processo produtivo, reduzir custos e permitir manutenções preditivas.
Dois dos padrões mais utilizados nesse contexto são o WS e o PackML. Embora ambos tenham como objetivo estruturar o comportamento de máquinas, suas abordagens e níveis de detalhamento são bastante distintos — e isso se reflete diretamente na forma como impactam em um cálculo como o de OEE.
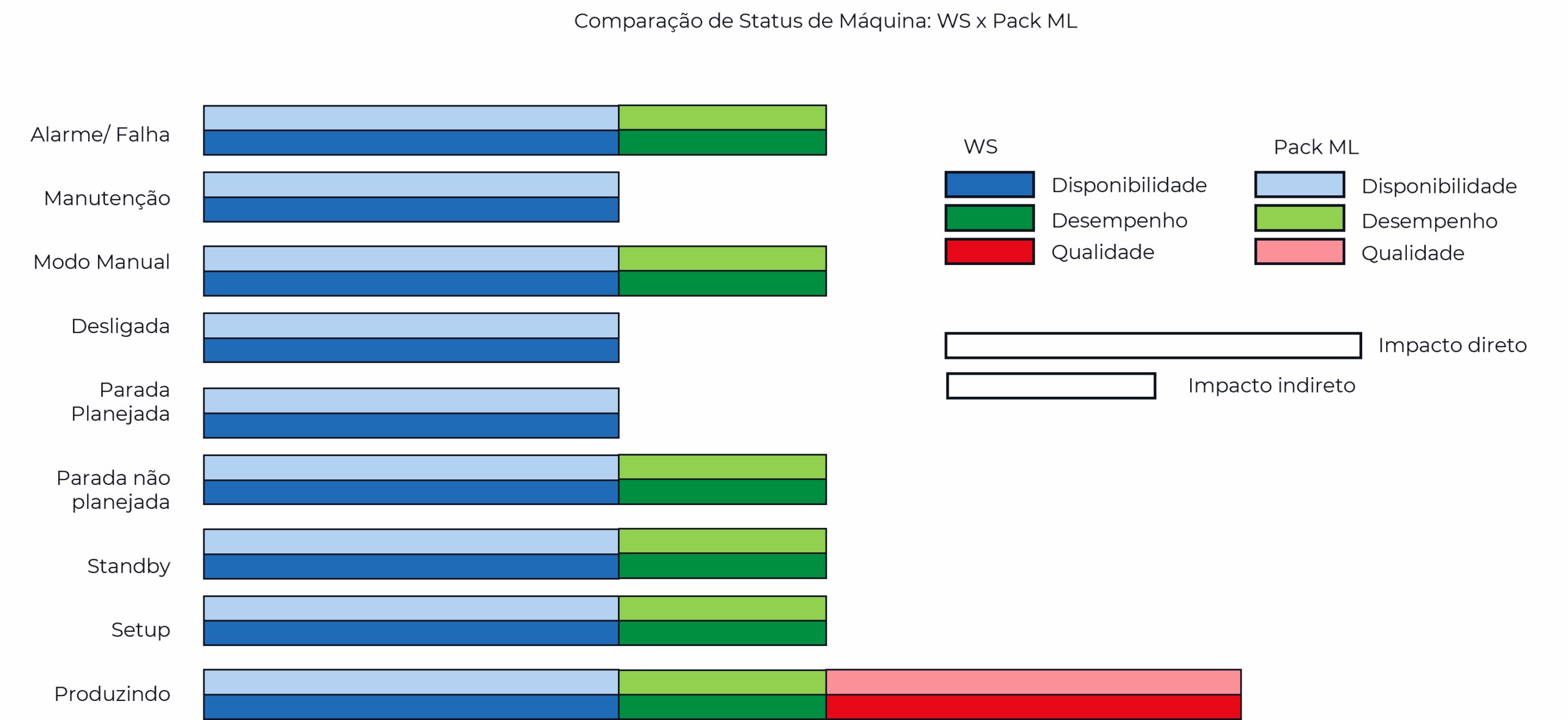
A visualização comparativa entre os padrões evidencia essa diferença. Cada linha representa um estado de máquina do WS, com seu equivalente funcional no PackML. As barras segmentadas por cor — azul para disponibilidade, verde para desempenho e vermelho para qualidade — mostram como cada estado contribui para os três pilares do OEE.
Comparando os tons das cores do gráfico, o que salta aos olhos é a granularidade do WS. Enquanto o PackML agrupa comportamentos similares em estados como Held, Suspended e Aborted, o WS os separa em categorias como Parada Planejada, Parada Não Planejada, Modo Manual e Alarme/Falha. Essa subdivisão permite capturar nuances operacionais com mais precisão, atribuir impactos distintos a cada tipo de parada e melhorar a rastreabilidade e a análise de causas de perda.
Por exemplo, no WS, Parada Planejada e Parada Não Planejada são estados distintos, com impactos diferentes no OEE. Já no PackML, ambos podem ser representados por estados genéricos, sem distinção explícita da causa. Isso não é uma limitação, mas sim uma consequência do foco funcional de cada padrão.
O WS é orientado à padronização de dados para análise de produção, com foco em KPIs, relatórios e integração com sistemas supervisórios. Já o PackML é voltado à automação e controle de máquinas, e prioriza a interoperabilidade entre equipamentos e a lógica de estados para controle de sequência. Por isso, o WS precisa ser mais detalhado — ele responde a perguntas como: Qual tipo de parada mais afeta a disponibilidade? Qual modo de operação está associado à maior perda de qualidade? Como o tempo de setup impacta o desempenho?
Essa comparação mostra como diferentes arquiteturas de controle e padronização influenciam a forma como os dados são interpretados e utilizados para melhoria contínua, eficiência operacional e tomada de decisão baseada em dados.
Saiba mais sobre a ST-One.