El 86% de las emisiones de dióxido de carbono en Brasil son el resultado de la quema de combustibles fósiles para la producción de energía y materiales, según el diario O Globo (2021). En respuesta a esta realidad, el 27% de las industrias del país ya se han comprometido con la carbono neutralidad, con objetivos de reducción de emisiones de carbono. Además de que este cambio de actitud es beneficioso para el problema climático global, contribuye a aumentar la productividad, la calidad del producto y garantiza que las industrias cumplan con las regulaciones gubernamentales requeridas.
Una industria manufacturera utiliza gases en varias etapas del proceso de producción, especialmente en el funcionamiento de calderas. Este tipo de equipos transforman la energía del combustible en energía térmica, calentando el agua depositada en sus tanques y produciendo vapor. Algunos de los procesos industriales más comunes para el uso de vapor son el calentamiento directo e indirecto, la pasteurización, la esterilización y el proceso de secado. Para satisfacer la demanda, existen diferentes tipos de calderas industriales, tales como:
- Tubos de fuego: Se caracterizan por una configuración en la que los gases emitidos pasan a través de los tubos, mientras que el agua permanece en tubos. Son ideales para la generación de vapor de hasta 30 toneladas/h y son conocidos por su rápida adaptabilidad a la demanda cambiante de vapor. También son capaces de utilizar varios tipos de combustibles, incluida la biomasa;
- Tubos de agua: En este caso, el agua circula por el interior de las tuberías, mientras que los gases resultantes de la combustión están en el exterior. La industria lo utiliza para la generación de electricidad, debido a su capacidad para soportar altas presiones y generar grandes cantidades de vapor.
- Recuperación de calor: Están diseñados para aprovechar el calor residual de procesos industriales como turbinas, motores y hornos. Este calor genera vapor, que se puede aplicar en la calefacción industrial, por ejemplo.
Ruta de vapor en procesos industriales
La elección del combustible que se utilizará es uno de los factores que más impacta en las emisiones de gases. Los combustibles renovables, como la biomasa, el biogás, los aceites vegetales y los residuos industriales, son alternativas sostenibles para la combustión en calderas industriales. Ayudan a reducir las emisiones de dióxido de carbono y promueven la sostenibilidad, y suelen ser más rentables y accesibles.
Por mucho que las pérdidas de eficiencia durante la distribución de vapor, o procesos posteriores específicos, puedan causar la emisión de gases, la generación de vapor en las calderas es la principal culpable. Para que el vapor cumpla su objetivo, pasa por al menos los siguientes pasos:
- Generación de vapor en la caldera: El proceso comienza con la caldera, donde se queman combustibles (fósiles o renovables) para calentar el agua. El agua caliente se convierte en vapor.
- Distribución de vapor: El vapor generado se distribuye a través de una red de tuberías. Estas tuberías están diseñadas para mantener la presión y la temperatura del vapor, asegurando que llegue a los puntos de uso de manera eficiente.
- Control y Regulación: Antes de llegar a los procesos específicos, el vapor pasa a través de válvulas de control y regulación que ajustan su presión y temperatura según sea necesario para cada aplicación.
- Uso en Procesos Industriales:
- Calentamiento directo e indirecto: El vapor se utiliza para calentar materiales directamente o a través de intercambiadores de calor.
- Pasteurización y esterilización: En la industria de alimentos y bebidas, el vapor se utiliza para pasteurizar y esterilizar productos, garantizando su seguridad y calidad.
- Movimiento de la turbina: En las centrales eléctricas, el vapor mueve las turbinas para generar electricidad.
- Secado: El vapor se utiliza para secar materiales, como la madera y el papel, asegurando la calidad del producto final.
- Limpieza: En lavanderías industriales y otras aplicaciones, el vapor se utiliza para una limpieza profunda y eficiente.
- Condensación y retorno: Después de ser utilizado, el vapor se condensa y vuelve a un estado líquido. Este condensado puede ser reciclado y enviado de vuelta a la caldera para ser calentado de nuevo, cerrando el ciclo y aumentando la eficiencia energética.
Tipos de gases en el proceso de creación de vapor en una caldera industrial
Debido a la influencia tanto en la productividad como en la calidad del producto, es necesario medir los tipos de gases emitidos. El primer paso es la instalación de analizadores de gases, siendo el infrarrojo (IR) y la espectrometría de masas (SM) los más utilizados. A continuación, es necesario utilizar tecnologías que lean estos sensores y almacenen la información recopilada en una base de datos. Al medir la composición de los gases, en tiempo real, es posible explorar el análisis de datos y tener nuevos conocimientos para mejorar el rendimiento de las calderas. El último paso es realizar los ajustes necesarios en las calderas.
Cada tipo de gas indica algo sobre el proceso de producción. Los niveles inadecuados de oxígeno (O2) ayudan a determinar si hay exceso o falta de aire en la combustión o problemas en la mezcla de combustible y aire. El dióxido de carbono (CO2) está relacionado con la cantidad de combustible quemado, los altos niveles de este gas indican que la combustión fue completa. El monóxido de carbono (CO) indica la eficiencia de la producción, ya que es un subproducto peligroso de la combustión incompleta. El óxido de nitrógeno (NOX) es un contaminante importante, por lo que su medición es importante para evaluar el impacto ambiental. Por último, el dióxido de azufre (SO2) es relevante en calderas que utilizan combustibles fósiles, su alta presencia indica el uso de combustible de baja calidad.
El Potencial de Calentamiento Global (GWP, por sus siglas en inglés) tiene criterios para medir el impacto de cada gas de efecto invernadero. Compara la capacidad de retención de calor de un gas con el dióxido de carbono durante un período específico. En las industrias, esto se divide en tres categorías: Alcance 1 (producido directamente por la empresa), Alcance 2 (generado por energía y otros recursos), Alcance 3 (resultante de fuentes indirectas en la cadena de suministro).
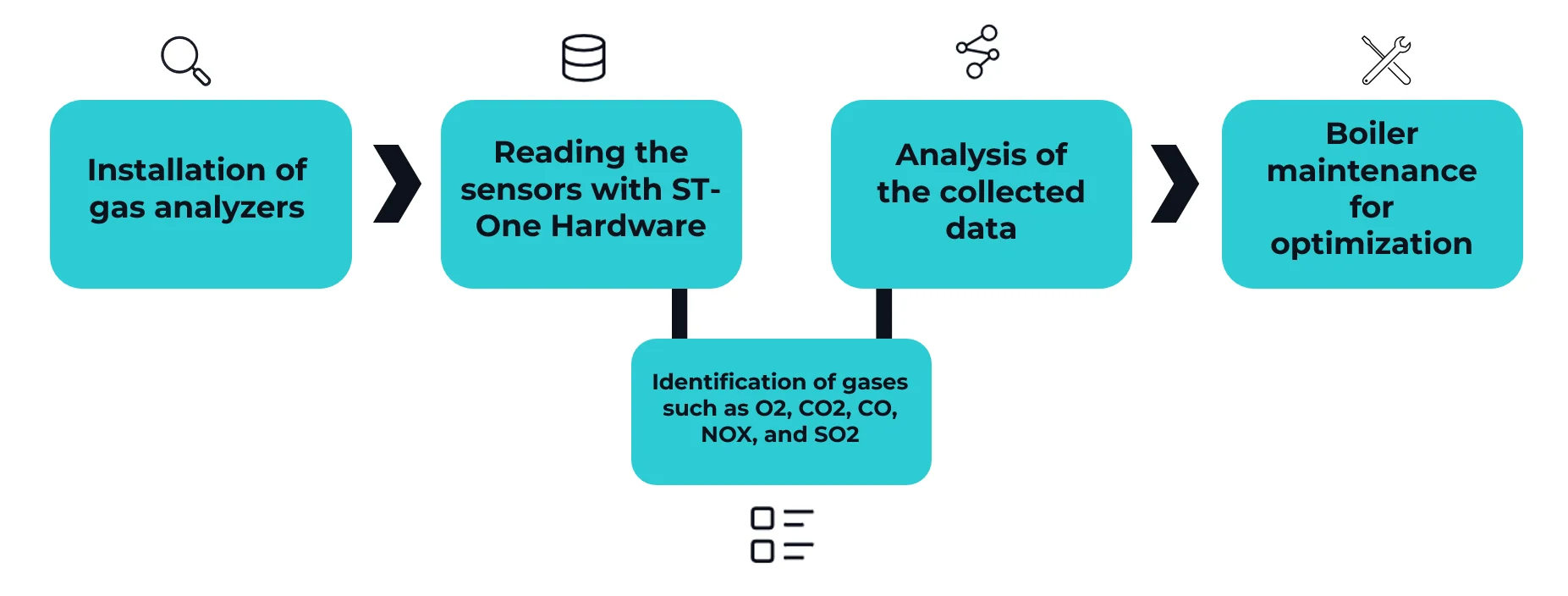
Creación de vapor: eficiencia en calderas industriales
La recopilación de datos centrada en la emisión de gases en una caldera permite realizar diversos tipos de análisis, imprescindibles para garantizar la eficiencia energética, el cumplimiento normativo y la sostenibilidad medioambiental. Entre los principales análisis se encuentran el análisis de gases de escape, que mide contaminantes como CO₂, CO, NOₓ y SO₂, identificando los problemas de combustión y la necesidad de mantenimiento. La prueba de combustión, que monitorea la eficiencia y la presencia de gases contaminantes, permitiendo ajustes en la relación aire-combustible y la temperatura de la llama. Y la termografía detecta puntos calientes, lo que indica problemas de aislamiento e ineficiencias en la transferencia de calor.
Además de estos análisis específicos, es esencial el análisis de la eficiencia de la caldera. Para realizar este análisis, primero es necesario entender cómo se calcula: hay dos métodos principales: el método directo y el método indirecto (o método de pérdida).
Método directo
El método directo calcula la eficiencia de la caldera en función de la relación entre la energía útil generada y la energía suministrada por el combustible. La fórmula es:
Eficiência (%)= (Q×(H−h) / q×GCV)×100
Dónde:
- Q = Potencia calorífica en kJ
- H = Entalpía de vapor en kJ/kg
- h = Entalpía del agua de alimentación en kJ/kg
- q = Consumo de combustible en kg
- GCV = Poder calorífico bruto del combustible en kJ/kg
Método indirecto (o método de pérdida)
El método indirecto calcula la eficiencia de la caldera considerando las pérdidas de energía. Las principales pérdidas incluyen:
- Pérdidas de calor en los gases de combustión
- Pérdidas de calor debidas a la humedad en el combustible
- Pérdidas de calor debidas a la humedad en el aire de combustión
- Pérdidas de calor debidas a la radiación y la convección
La fórmula general para el método indirecto es: Eficiencia (%)=100−Pérdidas totales (%)
Indicadores de Desempeño para el cálculo de Eficiencia en Calderas Industriales
El análisis del rendimiento de los sistemas de generación de vapor implica varios factores que impactan directamente en la eficiencia, seguridad y sostenibilidad del proceso. Uno de los principales indicadores es la relación entre el vapor producido y el volumen de combustible consumido, lo que permite evaluar la cantidad de vapor generado por unidad de combustible, reflejando directamente la eficiencia del sistema. La temperatura del agua de alimentación también es clave, ya que cuanto más caliente está esta agua, menos energía se necesita para convertirla en vapor, lo que contribuye a una operación más eficiente. Otro aspecto relevante es el poder calorífico del combustible, ya que los combustibles con una mayor capacidad de liberación de energía por unidad de masa son naturalmente más eficientes.
Además, el caudal de los gases de escape debe controlarse cuidadosamente, ya que los caudales excesivos pueden indicar pérdidas de calor significativas, lo que reduce el rendimiento general del sistema. El aislamiento térmico juega un papel crucial en este contexto: un buen aislamiento evita la pérdida de calor por radiación y convección, manteniendo la energía dentro del sistema. La regulación de la combustión, a su vez, debe ajustarse para asegurar la proporción ideal entre aire y combustible, optimizando la combustión y evitando excesos que resulten en pérdidas o aumento de contaminantes.
A partir de estos análisis, es posible extraer información valiosa para la operación y el mantenimiento del sistema. La optimización de la combustión, por ejemplo, permite mejorar la relación aire-combustible y controlar la temperatura de la llama, lo que se traduce en una mayor eficiencia y menores emisiones contaminantes.
Impacto de la ciencia de datos en la gestión de emisiones industriales
Según el Boston Consulting Group (2023), el uso de la Ciencia de Datos tiene el potencial de evitar la emisión de 2,6 a 5,3 gigatoneladas de CO2. En un contexto global, esto representa una reducción del 5% al 10% de las emisiones previstas por el Acuerdo de París.
Además, es un aliado importante para aspectos relacionados con ESG (Environmental, Social and Governance). En la parte medioambiental, además de reducir los gases contaminantes, actúa para optimizar el uso de los recursos naturales, como el agua y la energía. También ayuda en la implementación de sistemas de logística inversa, facilitando la reutilización de materiales e impactando en la reducción de costos.
En el aspecto social, el uso de esta tecnología para reducir los contaminantes mejora la salud y la seguridad de los empleados y las comunidades cercanas a las fábricas. Esto demuestra un compromiso con el bienestar social.
Por último, en materia de gobernanza, el seguimiento de las emisiones demuestra transparencia, lo que mejora la reputación del sector y aumenta la confianza de los inversores. Además, es capaz de identificar riesgos operacionales.
En resumen, el análisis de emisiones de calderas es beneficioso para las industrias de muchas maneras. La ciencia de datos permite identificar los diferentes gases producidos, y analizar el nivel de cada uno para descubrir puntos de mejora en la caldera. A partir de esto, la industria puede actuar para aumentar la productividad, además de cumplir con las leyes de protección ambiental. Más información sobre ST-One .