86% of carbon dioxide emissions in Brazil are the result of the burning of fossil fuels for the production of energy and materials, according to the newspaper O Globo (2021). In response to this reality, 27% of the country’s industries have already made a commitment to carbon neutrality, with targets to reduce carbon emissions. In addition to this change in attitude being beneficial to the global climate issue, it contributes to increased productivity, product quality and ensures that industries are in compliance with the required government regulations.
A manufacturing industry uses gases in various stages of the production process, especially in the operation of boilers. This type of equipment transforms the energy of the fuel into thermal energy, heating the water deposited in its tanks and producing steam. Some of the most common industrial processes for using steam are direct and indirect heating, pasteurization, sterilization, and the drying process. To meet the demand, there are different types of industrial boilers, such as:
- Fire Tubes: They are characterized by a configuration in which the emitted gases pass through the tubes, while the water stays in tubes. They are ideal for steam generation up to 30 tons/h, and are known for their rapid adaptability to changing steam demand. They are also able to use various types of fuels, including biomass;
- Water tubes: In this case, the water circulates inside the pipes, while the gases resulting from combustion are outside. The industry uses it for the generation of electricity, due to its ability to withstand high pressure and generate high amounts of steam.
- Heat recovery: They are designed to harness waste heat from industrial processes such as turbines, motors, and furnaces. This heat generates steam, which can be applied in industrial heating, for example.
Steam Path in Industrial Processes
The choice of which fuel will be used is one of the factors that most impacts gas emissions. Renewable fuels, such as biomass, biogas, vegetable oils, and industrial waste, are sustainable alternatives for burning in industrial boilers. They help reduce carbon dioxide emissions and promote sustainability, and are often more cost-effective and accessible.
As much as efficiency losses during steam distribution, or specific subsequent processes can cause the emission of gases, the generation of steam in boilers is the main culprit. For the steam to fulfill its objective, it goes through at least the following steps:
- Steam Generation in the Boiler: The process begins with the boiler, where fuels (fossil or renewable) are burned to heat the water. The heated water turns into steam.
- Steam Distribution: The steam generated is then distributed through a network of pipes. These pipes are designed to maintain the pressure and temperature of the steam, ensuring that it reaches the points of use efficiently.
- Control and Regulation: Before reaching the specific processes, the steam passes through control and regulation valves that adjust its pressure and temperature as needed for each application.
- Use in Industrial Processes:
- Direct and Indirect Heating: Steam is used to heat materials directly or through heat exchangers.
- Pasteurization and Sterilization: In the food and beverage industry, steam is used to pasteurize and sterilize products, ensuring their safety and quality.
- Turbine Movement: In power plants, steam moves turbines to generate electricity.
- Drying: Steam is used to dry materials, such as wood and paper, ensuring the quality of the final product.
- Cleaning: In industrial laundries and other applications, steam is used for deep and efficient cleaning.
- Condensation and Return: After being used, the vapor condenses and returns to a liquid state. This condensate can be recycled and sent back to the boiler to be heated again, closing the cycle and increasing energy efficiency.
Types of Gases in the Process of Creating Steam in an Industrial Boiler
Due to the influence on both productivity and product quality, it is necessary to measure the types of gases emitted. The first step is the installation of gas analyzers, with infrared (IR) and mass spectrometry (SM) being the most commonly used. Next, it is necessary to use technologies that read these sensors, and store the information collected in a database. By measuring the composition of the gases, in real time, it is possible to explore data analysis and have new insights to improve the performance of the boilers. The last step is to make necessary adjustments to the boilers.
Each type of gas indicates something about the production process. Inadequate oxygen (O2) levels help determine if there is excess or lack of air in combustion or problems in the fuel-air mixture. Carbon dioxide (CO2) is related to the amount of fuel burned, high levels of this gas indicate that the burning was complete. Carbon monoxide (CO) indicates the efficiency of production, as this is a dangerous by-product from incomplete combustion. Nitrogen oxide (NOX) is a significant pollutant, so its measurement is important for assessing environmental impact. Finally, sulfur dioxide (SO2) is relevant in boilers that use fossil fuels, its high presence indicates the use of low-quality fuel.
The Global Warming Potential (GWP) has criteria to measure the impact of each greenhouse gas. It compares the heat-holding capacity of a gas to carbon dioxide for a specific period. In industries, this falls into three categories: Scope 1 (produced directly by the company), Scope 2 (generated by energy and other resources), Scope 3 (resulting from indirect sources in the supply chain).
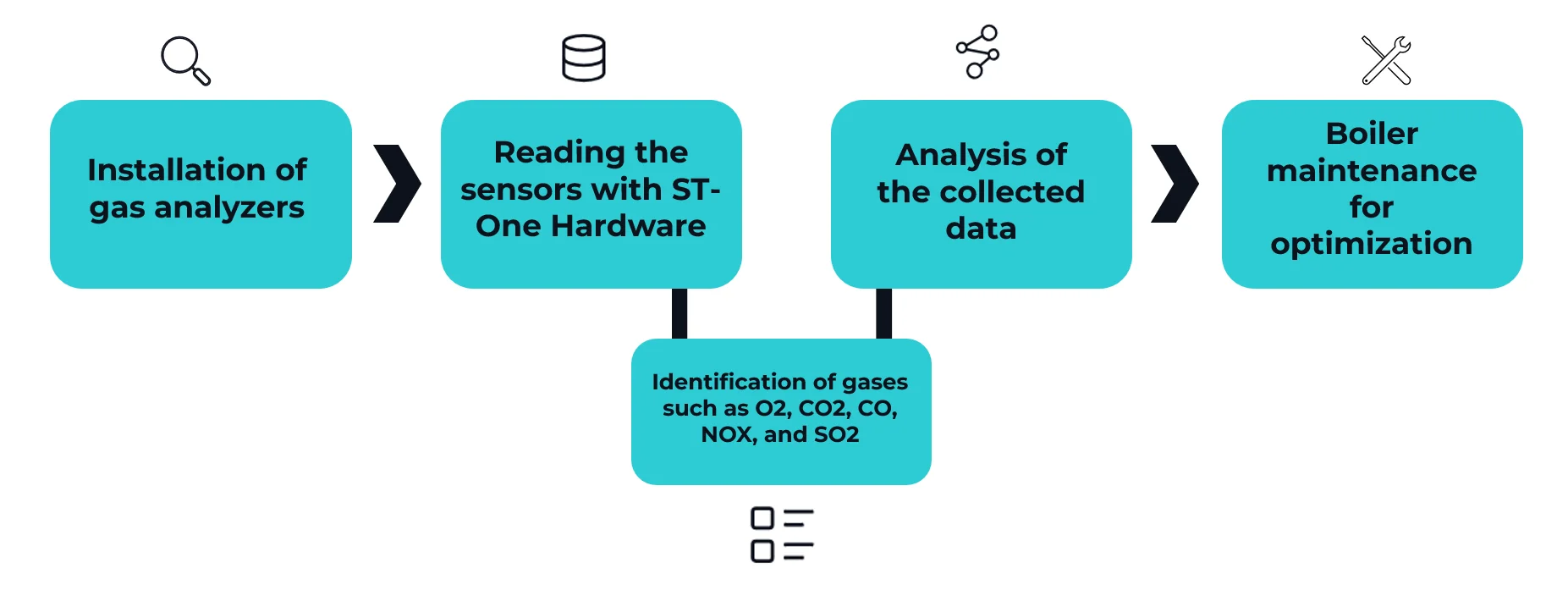
Steam Creation: Efficiency in Industrial Boilers
Data collection focused on the emission of gases in a boiler allows for various types of analysis, essential to ensure energy efficiency, regulatory compliance and environmental sustainability. Among the main analyses are the exhaust gas analysis, which measures pollutants such as CO₂, CO, NOₓ and SO₂, identifying combustion problems and the need for maintenance. The combustion test, which monitors the efficiency and the presence of polluting gases, allowing adjustments in the air-fuel ratio and flame temperature. And thermography detects hot spots, indicating insulation problems and inefficiencies in heat transfer.
In addition to these targeted analyses, boiler efficiency analysis is essential. To perform this analysis, it is first necessary to understand how it is calculated: there are two main methods: the direct method and the indirect method (or loss method).
Direct Method
The direct method calculates the efficiency of the boiler based on the ratio of the useful energy generated to the energy supplied by the fuel. The formula is:
Efficiency (%)= (Q×(H−h) / q×GCV)×100
Where:
- Q = Heat output in kJ
- H = Enthalpy of steam in kJ/kg
- h = Feedwater enthalpy in kJ/kg
- q = Fuel input in kg
- GCV = Gross Calorific Value of fuel in kJ/kg
Indirect Method (or Loss Method)
The indirect method calculates the efficiency of the boiler considering energy losses. The main losses include:
- Heat losses in flue gases
- Heat losses due to moisture in the fuel
- Heat losses due to moisture in the combustion air
- Heat losses due to radiation and convection
The general formula for the indirect method is: Efficiency (%)=100−Total Losses(%)
Performance Indicators for the calculation of Efficiency in Industrial Boilers
The performance analysis of steam generation systems involves several factors that directly impact the efficiency, safety and sustainability of the process. One of the main indicators is the ratio between the steam produced and the volume of fuel consumed, which allows the amount of steam generated per unit of fuel to be evaluated, directly reflecting the efficiency of the system. The temperature of the feed water is also key, as the hotter this water is, the less energy it takes to turn it into steam, contributing to a more efficient operation. Another relevant aspect is the calorific value of the fuel, since fuels with a higher energy release capacity per unit mass are naturally more efficient.
In addition, the flow rate of the exhaust gases must be carefully monitored, as excessive flow rates can indicate significant heat losses, reducing the overall performance of the system. Thermal insulation plays a crucial role in this context: good insulation prevents heat loss through radiation and convection, keeping energy inside the system. The burning regulation, in turn, must be adjusted to ensure the ideal proportion between air and fuel, optimizing combustion and avoiding excesses that result in losses or increase in pollutants.
Based on these analyses, it is possible to extract valuable information for the operation and maintenance of the system. Combustion optimization, for example, makes it possible to improve the air-fuel ratio and control the temperature of the flame, resulting in greater efficiency and lower pollutant emissions.
Impact of Data Science on Industrial Emissions Management
According to the Boston Consulting Group (2023), the use of Data Science has the potential to avoid the emission of 2.6 to 5.3 gigatons of CO2. In a global context, this represents a reduction of 5% to 10% of the emissions foreseen by the Paris Agreement.
In addition, it is an important ally for aspects related to ESG (Environmental, Social and Governance). In the environmental part, in addition to reducing polluting gases, it acts to optimize the use of natural resources, such as water and energy. It also assists in the implementation of reverse logistics systems, facilitating the reuse of materials and impacting cost reduction.
On the social side, the use of this technology to reduce pollutants improves the health and safety of employees and communities near the factories. This demonstrates a commitment to social welfare.
Finally, in governance, emissions monitoring demonstrates transparency, which improves the industry’s reputation and increases investor confidence. In addition, it is capable of identifying operational risks.
In short, boiler emission analysis is beneficial to industries in many ways. Data science allows you to identify the different gases produced, and analyze the level of each one to discover points of improvement in the boiler. From this, the industry can act to increase productivity, in addition to complying with environmental protection laws. Learn more about ST-One .